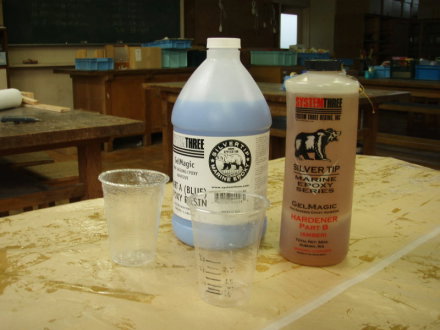 |
今回新規にエポキシ接着剤として購入したシステムスリー社の新製品のジェルマジックです。利点はフィラーが不要であることと,汎用エポキシ樹脂で付けるよりも強度が高いとのことです。但し、臭いが汎用のものより強く指につくと荒れました。
|
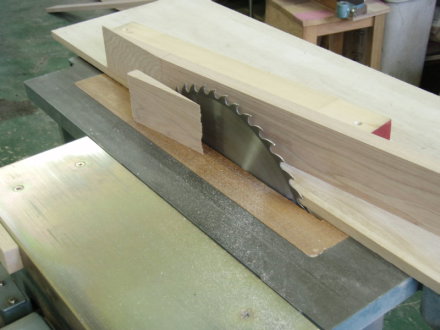 |
キールソンのスカーフジョイントのため、ご覧の縦切りジグ板にキールソンをフェンス材と共に固定し、スカーフのテーパーを付けます。結果、非常に綺麗に接合面を切り出すことが出来ました。
|
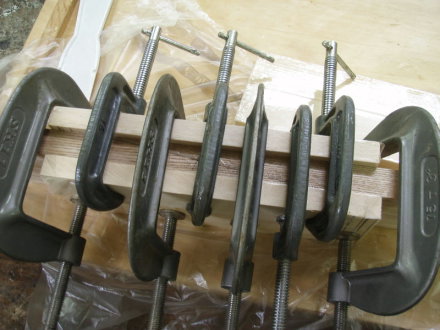 |
25mm厚x70mm幅x3100mm長のキールソン(キールソン)材のスカーフジョイントをしているところです。スカーフは1:8の比です。
|
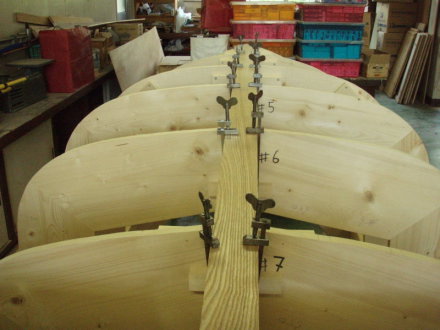 |
出来たキールソンをモールド上の取り付け位置に仮置きしました。
|
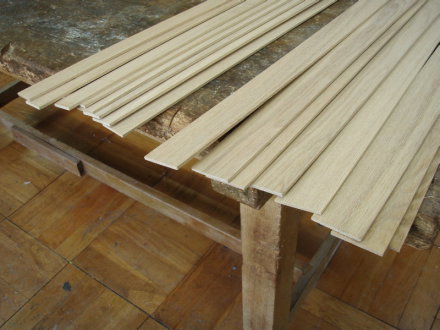 |
ステム材は積層にするため4mm厚x50mm幅x1000mm長のタモ材のストリップ材を切り出しました。鋸代は2mmで、4mm厚のストリップ材ですから、その製材効率は66%と悪く大鋸屑が34%出る計算になります。
|
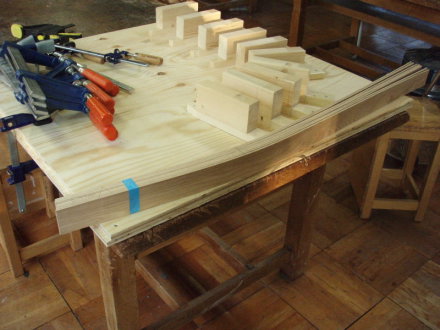 |
ご覧の写真がアジャスタブル積層ジグになります。合板に積層するカーブをトレース、その線上にブロックを置きネジ留めします。
|
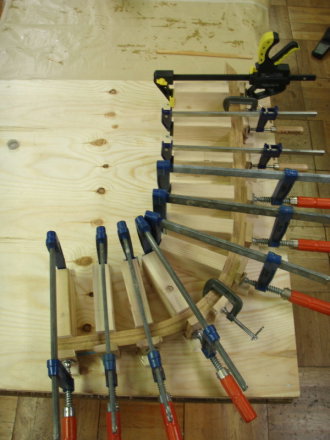 |
写真は先ずインナーステムの積層をしているところです。クランプの順番はカーブのキツイ方から順に緩いほうへと閉めていきます。
|
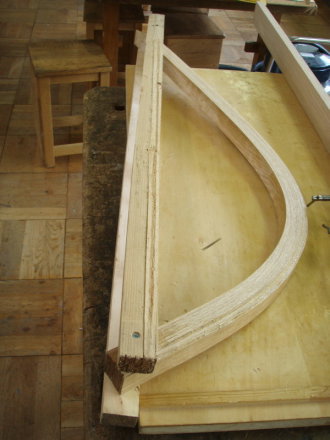 |
翌日積層が固まったので、その外面にセロハンテープをはり、更にその外側にアウターステムの積層をやりました。
|
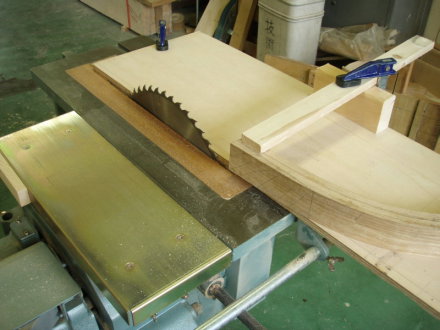 |
今度は積層したステム材のキールソンとの接合部をテーパー切りしました。ご覧の通り、こちらも縦きりジグ板にステム材を載せクランプでしっかり固定すると綺麗な切り口で仕上がります。
|
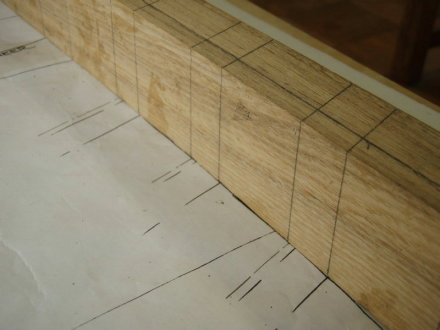 |
インナーステムの内面、両側面、前面にプランク材のラップランド(プランクがオーバーラップする幅)を原寸図から墨付しています。
|
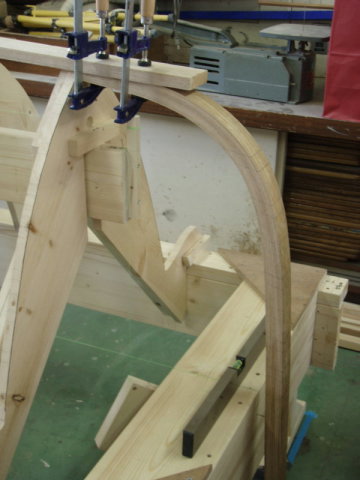 |
出来たインナーステムをビルディングジグと一番モールドに取り付けカーブの出来具合をチェックしました。結果図面通りに出来ていました。
|
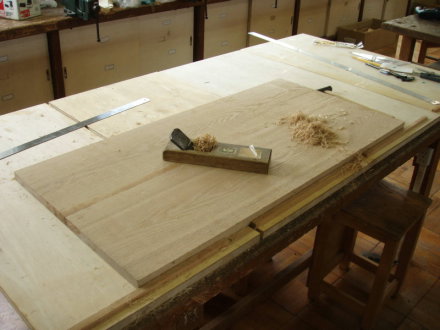 |
トランサムは22mm厚x500mm幅x1000mm長のタモ板がいるのでご覧の通り、二枚のタモ板を接ぎ合わせました。しかし板目の堅木はどうしても反りが出るので、鉋で横擦りで平面を出して行きます。
|
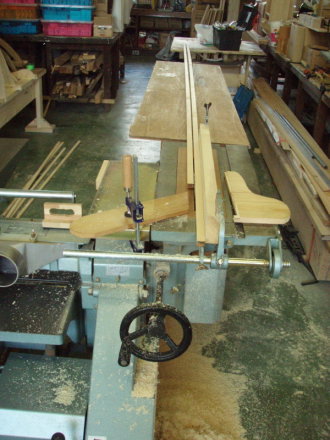 |
今度はモールド間のフェアカーブ度を確かめるため、ラップランドと同じ幅の12mm厚x19mm幅x4000mm長のストリンガー材を30mm厚x40mm厚x4m長の北洋赤松材からテーブルソーを使用して切り出しました。
|
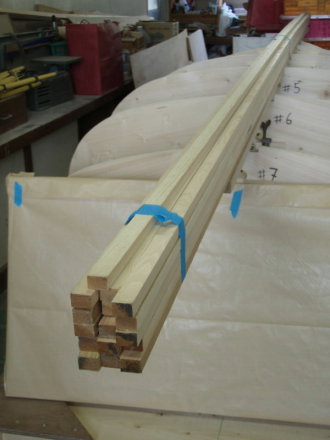 |
出来上がったストリンガーは、プランク材の数と同じ左右各8本都合16本を作成しました。
|
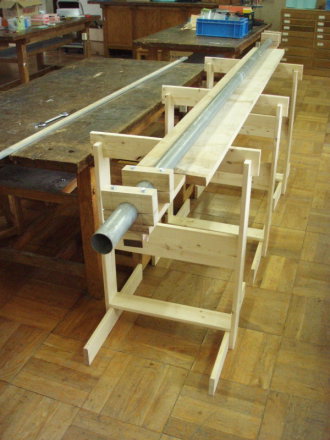 |
写真は足場パイプを利用して直線定規を自作したものです。以前より、1.8m長以上の合板や板材の直線切りに適切な定規がなくて苦労していました。今回Acornディンギーの製作では、2.2m,4m長の長材の縦切りや木端面削りが多く有り、この課題をどの様に解決しようかと思案しておりました。そんなときに、オーストラリアToriton社製のテーブルソーの延長テーブルを見てヒントを得ました。その延長テーブルは、やはり足場パイプの様な金属パイプ2を本平行に置くだけでの簡単な作りですが、精度良く縦切りが出来ていました。私は足場パイプ1本の両端に木製の特製クランプを自作し取り付けました。これによりパイプは材木上に強力に固定され直線定規に成ります。
|
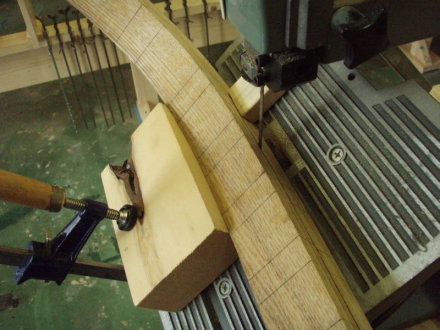 |
積層したステム材は出来ましたが、ビルディングジグに取り付けプランキングを始めるには、ステムの両側面にプランク材が隙間なく貼り付けられるようにプランク材ごとに角度切りする必要があります。ここではシェアー部の角度(一番鈍角)でステム全体をバンドソーで切り出しています。実際はプランク時に一枚づつバテンを使用して精密に角度をトリミングします。
|
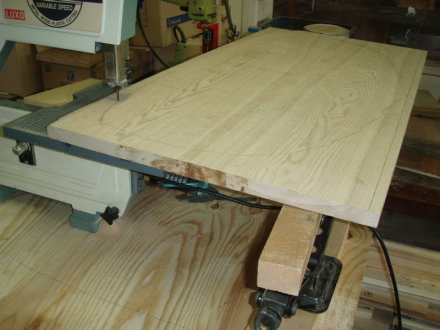 |
墨付けしておいたトランサム材をご覧の貧弱なバンドソーで内側外形線を切り出しています。このトランサム材は22mm厚x500mm幅x1000mm長のタモ材ですので結構重量があり、同バンドソーの小さいテーブルに安定して置くために自動車用ジャッキを利用した支持台を2個使用しています。
|
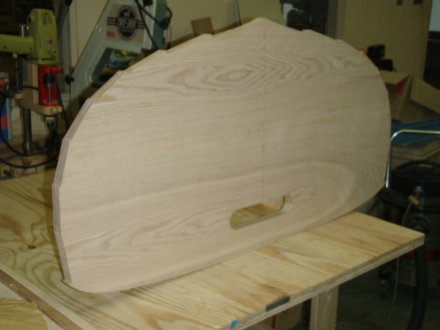 |
貧弱なバンドソーでしたが、何とかトランサムを切り出すことが出来ました。この内側外形線を最終的に出すためには、スキ鑿で慎重に墨線まで切り込みました。
|
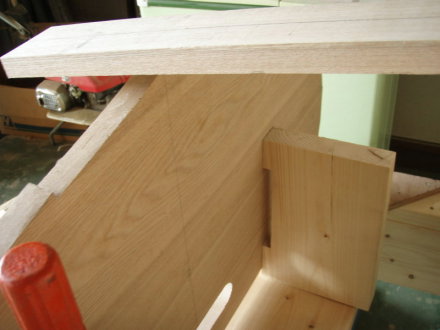 |
トランサム内側外形線の削り出しが出来たところで、写真にある様にトランサムを93度の角度で保持する為のブロックを2x8材で作り、上下2ヶ所を木工ボンドで接着しました。同保持ブロックはプランクが張り終わり、ターンオーバする時に内側から切り離します。
|
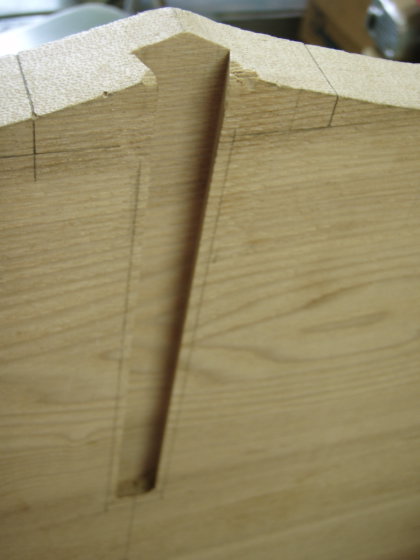 |
トランサム・ニーをトランサムに取り付けるのは木ネジとエポキシ接着剤が使われますが、トランサム表側にネジ穴を開けるのは少し格好良くなのと、タモ板目材のソリ防止(あまり期待できないかも)の理由で、私はご覧の様にニーのトランサム側の接合面にダブテールの溝を切りました。
ダブテールスライド部をルータで切ったニーをトランサムの溝に差し込んでいるところです。僅か溝幅が大きかったですが全体を差し込むとしっかり留まります。後はエポキシ接着剤を充填して完全に隙間がないようにして、取り付けます。
|
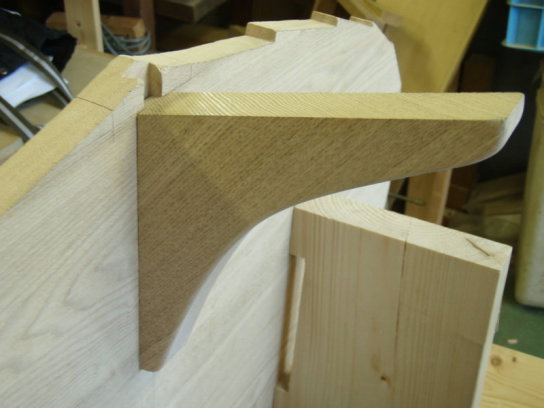 |
ニーをトランサムに完全に押入れ、ドライフィットで接合の具合を確認しています。
|
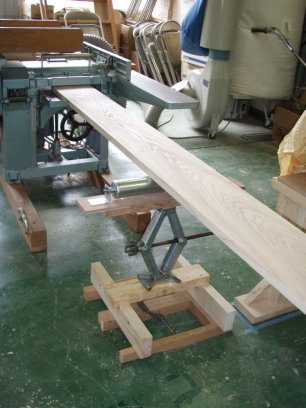 |
フルフレーム製作のため、27mm厚x220mm幅x2200mm長のタモ板を上下から自動鉋盤で削り、26mm厚にします。
|
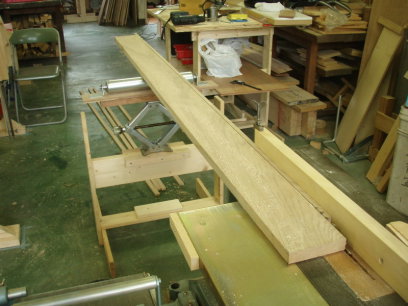 |
次にこの板を縦挽きするため、昇降盤のフェンスに当てる基準面を作ります。、以前製作した足場パイプ応用直線定規を用いてルータで直線を出します。その後、昇降盤でこのタモ板を13mm幅X26mm厚x2200mm長のストリップ材を12本縦挽きします。
|
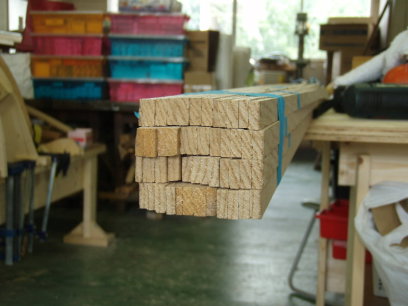 |
そして、この出来たストリップを90度回転させて更に4枚に挽割(5mm厚x13mm幅x2200mm長)引き割ります。写真は12本のストリップから都合48枚のフルフレーム積層板を作成しました。
|
|
モールドにフルフレームを取り付けるための駒留め作りました。1モールド当たり19個必要ですので、まだまだ足りません。
|
|
4番モールドにフルフレームを試験的に取り付けた状態です。フレーム幅が
12.5mmと狭いので50mmのCクランプのパッド部がフレームから外れ、役に立ちません。今回準備した75mm径の塩ビクランプが上手くフレーム積層版を締め付けています。
|
|
当初、フルフレームの製作は、積層曲げ(5mm厚x3層)で進めていましたが、三本目を過ぎた頃から積層板が割れ始めたため、急遽積層蒸し曲げに工法に変更しました。このためフルフレームを収納し蒸すことの出来る2.2m長の大きな蒸し器を製作しました。私の教科書(John
Brooks著 How to build glued Lapstrake wooden boatとGreg Rossel著 Building Small
Boat)には5ギャロンのガソリン携行缶をボイラーに使用してラジエータホースで蒸し器と接続しろとありましたので、半信半疑20Lタンクを購入しホースを解体屋から100円で入手し大変上手く大量の蒸気を作ることが出来ました。
|
|
積層板は5.5mm厚でしたので約15分の蒸しでOK、早速モールドに巻きつけるように曲げ付けましたが、いとも簡単に曲げを完了できました(ほぼ40秒以内)。
また、1番モールドのステムと接続するV字の厳しい曲げも写真の通り問題なく曲げ付けが出来ました。この後は、モールド間に1本づついるれフルフレームがまだ8本有ります。同様に蒸し器を使い、ストリンガーを巻きつけるように曲げ付をする予定です。
|
|
モールドに取り付けるフレームが出来たので、今度はトランサムの外面にオーナーのイニシャルをレターカービング(文字彫刻)しました。何分初めてのレターカービングですので、How-toDVDや木工雑誌で要領を勉強してやりましたが何とかできました。トランサムを取り外しいじれるのはこの時がが唯一のチャンスでした。
|